Global manufacturers demonstrate solid fourth industrial revolution initiatives
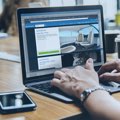
Annual joint World Economic Forum and McKinsey report highlights small group of global manufacturers at the forefront of technological innovation
Many manufacturers are piloting fourth industrial revolution initiatives, but few have managed to integrate the latest technologies at scale to realize significant economic and financial benefits, and instead, remain stuck in “pilot purgatory,” according to the World Economic Forum and McKinsey & Co.
Their newly released joint report, “Global Lighthouse Network: Insights from the Forefront of the Fourth Industrial Revolution” found that in 2019, 44 global factories showed leadership in the fourth industrial revolution.”
SEE: Digital transformation: An IT pro’s guide (free PDF) (TechRepublic)
The term refers to manufacturers that demonstrate digital manufacturing and globalization 4.0, and exhibit all of the essential characteristics of the fourth industrial revolution by utilizing automation, analytics, IoT and digitization, to connect their value chains end-to-end, according to the report.
Yet, at the same time, more than 70% of manufacturers around the world are falling further behind on their efforts to implement advanced manufacturing technologies, according to the report.
“We are seeing an increase of companies bringing 4IR into the heart of their operations, but the vast majority of organizations are not moving fast enough,” observed Enno de Boer, a partner and global leader of manufacturing at McKinsey & Co., USA, and one of the report’s authors. “By delaying the adoption of these technologies, organizations are going to find it increasingly difficult to catch up–the time is now for the manufacturing sector to embrace 4IR across the enterprise.”
The WEF and McKinsey studied more than 1,000 leading manufacturers of different sizes that “represent the leading edge of adopting technology at scale,” and conducted site visits to the “most advanced sites,” the report said.
Three technological megatrends that are principal drivers of this transformation in production are connectivity, intelligence and flexible automation, according to the report.
“There are increasing disparities in productivity, efficiency and growth between the leaders and the rest of the pack; we may soon end up with a bipolar scenario, with only winners and losers,” the report warned. “Delaying Fourth Industrial Revolution transformation is no longer a viable option. Companies that wish to remain competitive must embark on this journey.”
Lighthouses operate vastly different
Leading companies start by changing the way they operate as a business and go well beyond adding incremental digital tools, the report noted. “They simultaneously innovate their business processes, management systems, people systems and IoT/data systems,” the report said.
They may have taken different approaches to transformation, but they have demonstrated six key technological and human enablers, according to the report:
- Agile approach
- Agile digital studio
- IIoT [industrial IoT] stack
- Tech ecosystem
- IIoT academy
- Transformation office
The report delves into case studies of lighthouses, including China-based manufacturers Haier and SAIC Maxus, Phoenix Contact of Germany, and Schneider Electric in Batam.
Several of the lighthouses mentioned top skills that required training in Fourth Industrial Revolution plants, such as data analytics, technical equipment operational skills, use of 4IR technologies/digital tools; communication, collaboration and change management; and problem solving, the report notes.
“Notably, no Lighthouse executed Fourth Industrial Revolution transformation entirely on its own,” the report stated. “Each used partnerships, either to acquire new knowledge or collaborate in developing new knowledge.”
In fact, according to a 2019 survey, 55% of lighthouses are using partnerships with universities or other educational organizations to gain knowledge and talent,” the report said, and 71% of lighthouses have used internal academies and capability centers in some ways to build capabilities.
Call to action
The McKinsey and WEF report lists four recommendations for how the global lighthouse network can further strengthen its impact and footprint.
Observing that manufacturing accounts for 54% of the world’s energy consumption and is responsible for 20% of CO2 emissions globally, notably, the first recommendation is that the whole network achieve carbon-neutral manufacturing by 2025.
The second recommendation is that the network take SMEs under their wing. “Lighthouses need to exercise responsible leadership by actively supporting the diffusion of Fourth Industrial Revolution technologies through their entire production networks, which include suppliers of all sizes,” the report said.
It also advocates for investing capability building and lifelong learning and that the lighthouses network upgrade regulations, policies, and industrial development strategies to raise awareness of the 4IR among governments.
This article was updated on January 16, 2020.
Also see
Image: ipopba, Getty Images/iStockphoto