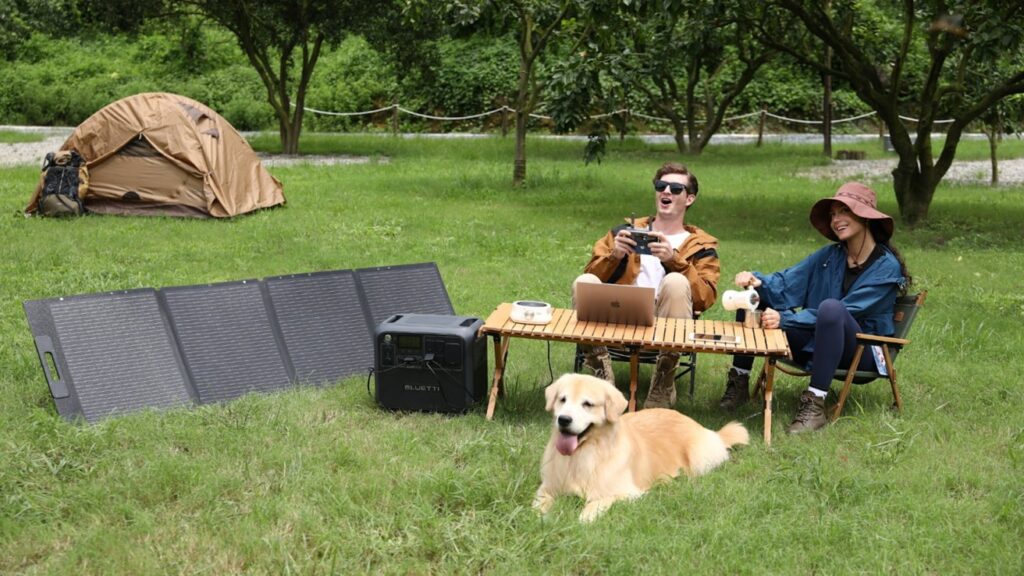
Even if you’re still relying on noisy gas generators, it isn’t too late to start switching to solar and battery solutions from Bluetti, and save big thanks to federal tax credits and trade-in subsidy.
Go green with Bluetti’s solar and portable power solutions
Switching to solar and battery-based energy in the U.S. can actually save you some money on taxes. And no, this isn’t something for the distant future — it’s happening right now.
Thanks to the U.S. Residential Clean Energy Credit, you can score a 30% federal tax credit on eligible solar systems and home batteries through 2032. So, with the right setup like the AC500 Home Battery Backup, you’re not just saving on your electricity bill — you could also get a portion of your purchase back when tax season rolls around.
Continue Reading on AppleInsider